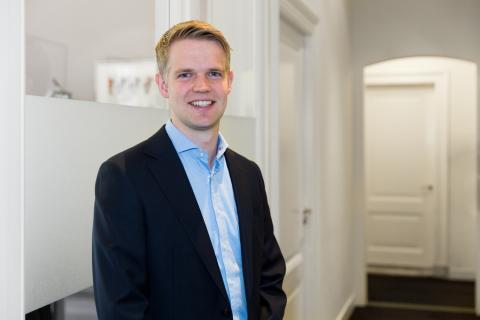
This time in "in the spotlight" colleague Johan den Breejen. Johan is part of the Solutions team within Districon. He will tell you all about his experiences.
Who are you?
My name is Johan den Breejen and I’m working for Districon for two years now. My background is in Econometrics and Operations Research, and I am part of the Solutions team within Districon. Within Solutions, we convert logistical questions to mathematical models, to enable us to approach problems from a mathematical point of view. We do this in such a way that the customers can use the models themselves on a daily, weekly or monthly base, to determine their optimal strategy.
In the two years that I am working with Districon, I have worked on a variety of projects. Currently, I’m working on three projects that are a nice representation of what we do: production planning, store replenishment and artificial intelligence.
My experiences
Production planning is a very nice problem to work on. It starts with visiting the production site to see how the product is made. Big machines that do complicated things, resulting (usually in high speed) in new products. The subject is fun and solving the problems is always a challenge (see also this link). The challenge mostly is in the complexity of the problem. There are a lot of different products that need to be made on several machines in a specific order. In such a case, you want to optimize multiple things at once: minimizing changeover time, limiting work in progress, efficiently using the machines and people, getting all your orders ready in time, etc. Optimizing everything at once usually has (too) long calculation times, so you need to be smart about how you want to use the computing power, to best support your planning. A great example of theory and practice coming together.
At our store replenishment project, the goal is to minimize the number of trucks used, but also to distribute the workload in the distribution center as best as possible over the week. The main decision variables are: “at which moments during a week do we replenish the store”, because from this decision the rest will follow almost automatically. From a mathematical point of view, this problem is less complex than production planning, but there are a lot of reasons that make certain solutions not usable in practice. Therefore, our approach is to make a relatively simple mathematical model. Then, we run many different scenario’s that are inspired by what works in practice. This way, the model stays understandable and we can really substantiate the resulting schedule for replenishing the stores.
Artificial intelligence is a whole new ball game, which I am working on within Districon for a while now. It’s been around for a lot longer and is already successfully applied to a lot of things around us. Lately, the need for artificial intelligence is also growing within logistics. More data is coming available and certain decisions need to be taken faster and faster. For example, you can see this in cutoff times, that keep getting set later in the day. Therefore, Districon is already experimenting with AI within logistics in several ways. The results are promising, and AI will definitely get a more prominent place within logistics. Besides optimization, we use (for a long time already) visualization of data in the form of Business Intelligence within Districon. AI will strengthen both fields. My role is to drive the application of AI at our customers. A fun and educational task to take upon me and a nice aspect of working with Districon, because they support me in these kinds of initiatives.
Which colleague will be in the spotlight next?
I would like to pass the pen to Robert de Zwart. Robert joined Districon just a few months earlier than me and lately we were sitting at the same table to discuss the future of AI within the Logistical world. I am looking forward to here about your experiences so far, Robert!